
19 Mar China’s steel sector could cut carbon emissions by more than 10% next year with faster shift to clean production: report
China’s steel sector could cut its greenhouse-gas emissions by over a tenth from current levels by next year if the country gets more ambitious about adopting cleaner production technology, according to US think tank Global Energy Monitor (GEM).
The emissions reduction – roughly the same as taking 47 million petrol-powered passenger vehicles off the road – would be possible if Beijing were to set a more ambitious target for the use of electric arc furnaces (EAFs) and accelerate its shift away from the dominant, coal-based process, known as blast furnace-basic oxygen furnace (BF-BOF), the organisation said in a report published on Tuesday.
Pushing EAF to 20 per cent of total production next year, rather than the current target of 15 per cent, could reduce the sector’s emissions by 11 per cent, versus 8.7 per cent with the lower target, GEM estimated.
“Given its outsized impact on carbon emissions, even incremental changes to the steel industry could significantly reduce China’s carbon footprint,” said Jessie Zhi, researcher at GEM and one of the authors of the report.
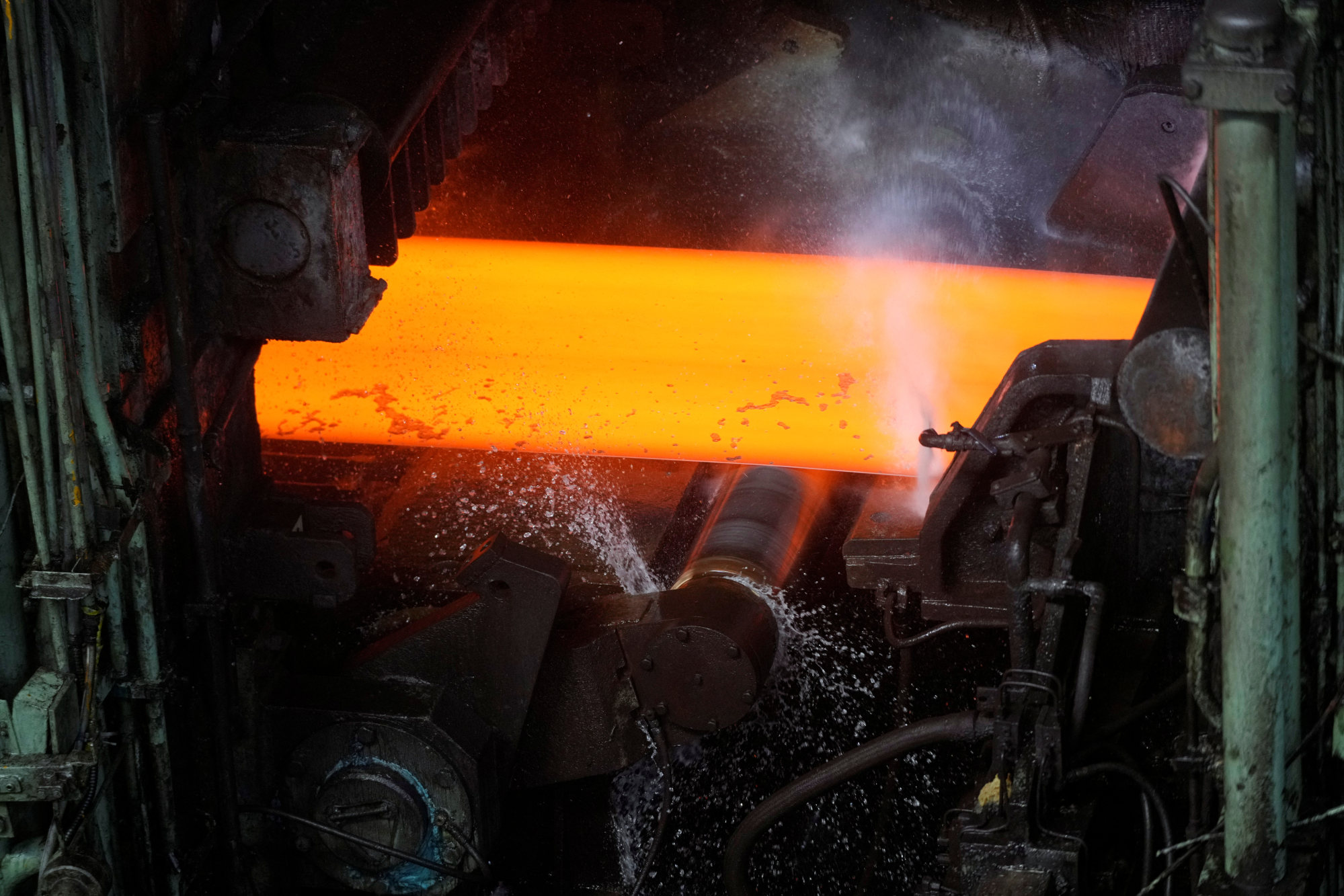
As of January, China had 1,064 million tonnes per annum (Mtpa) of steelmaking capacity, 86 per cent based on BF-BOF and 14 per cent using EAF, GEM’s data showed. That puts China just one percentage point away from the 2025 EAF target of 15 per cent, set by the Ministry of Industry and Information Technology (MIIT) in 2020.
While the 15 per cent target would reduce emissions by 179 Mtpa, raising the target to 20 per cent would eliminate 217 Mpta, or 21 per cent more emissions, according to Zhi.
China will miss its climate goals unless it reins in coal power: report
China will miss its climate goals unless it reins in coal power: report
The steel industry is China’s second biggest emitter of carbon dioxide after the power industry, accounting for between 15 and 20 per cent of the country’s overall emissions. The sector has long relied on the coal-based BF-BOF process, which emits about 2.1 tonnes of carbon dioxide per tonne of steel produced, compared with about 1.3 tonnes per tonne with EAF, according to GEM.
In a draft plan released by the MIIT in 2020, China originally called for EAF to account for from 15 to 20 per cent of steel production by 2025, but it removed mention of the 20 per cent level from guidance issued in 2022.
The country may aim to increase EAF’s share to more than 20 per cent by 2030, according to a proposal introduced this month by seven Chinese government apartments including the MIIT, the National Development and Reform Commission and the Ministry of Ecology and Environmental Protection.
China’s wind and solar power generation capacity to surpass coal in 2024
China’s wind and solar power generation capacity to surpass coal in 2024
“If China made modest adjustments to its current capacity development and closure plans to add more EAF capacity and less BF-BOF capacity, or retire more BF-BOF capacity and less EAF capacity, the country could install enough EAF capacity to make its initial ambition of reaching 20 per cent EAF production by 2025 possible, provided utilisation rates are raised,” said Caitlin Swalec, GEM’s programme director of heavy industry and one of the authors of the report.
This would require China to add around 39 Mtpa of new EAF capacity by 2025, GEM said, given that EAF is now on track to account for 15.9 per cent of China’s total crude steel production in 2025, or 151 Mtpa out of 950 Mpta.
While the common inputs for BF-BOF steelmaking are iron ore and coal, EAFs use scrap steel. Experts say raw materials make up 50 per cent of BOF cost and 75 per cent of EAF cost, with the difference between the costs of these inputs determining which is more expensive.